LEARNING TOGETHER IN THE LEAN LAB: THREE COMPANIES, ONE TRAINING COURSE
- 20.12.2024
- General
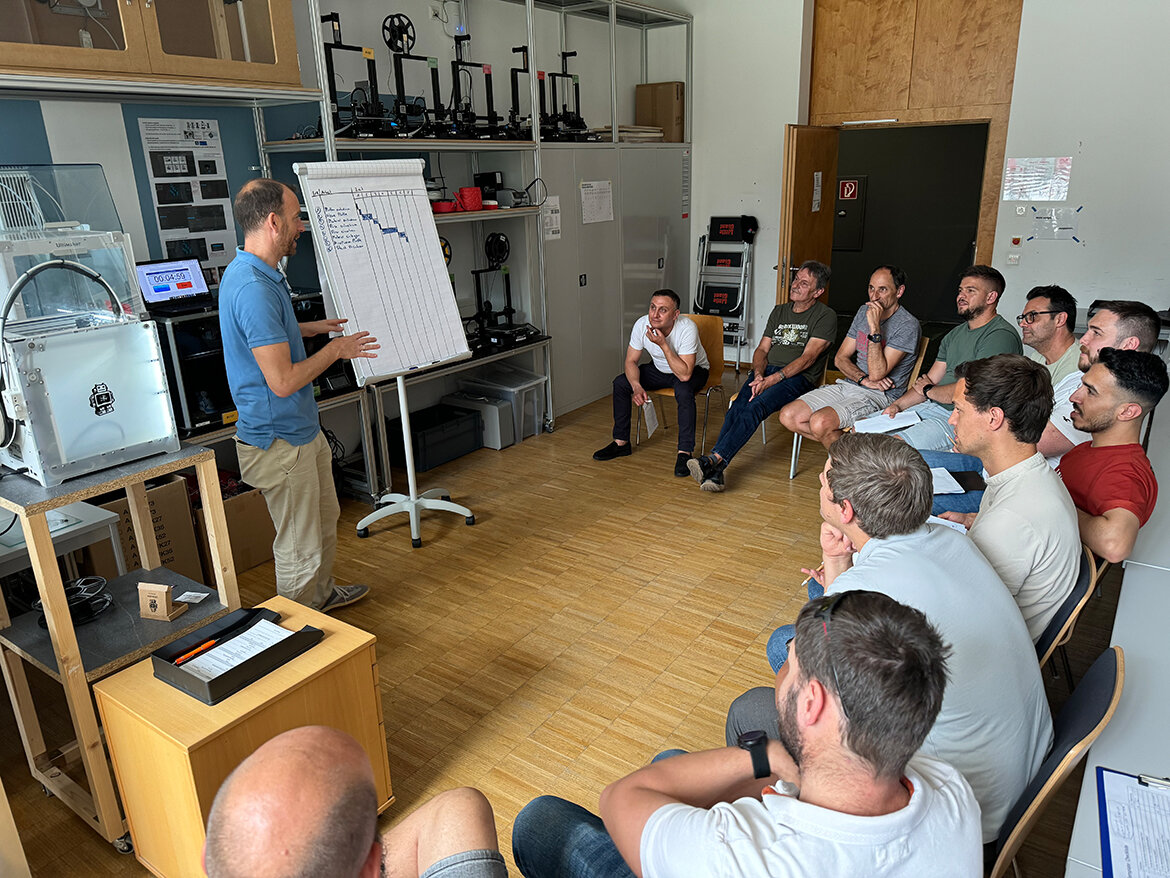
Employees from the companies Freudenberg, Pirlo and STHIL are working on solutions together with Markus Ehrlenbach, MSc from the Kufstein University of Applied Sciences.
Employees from Freudenberg Sealing Technologies, Pirlo and STHIL Austria were trained in the LEAN Lab at the Kufstein University of Applied Sciences to improve flexibility in their production facilities. They not only learnt with, but also from each other.
These are problems that many companies are facing: Customers are only placing smaller order quantities, but more frequently and product diversity is increasing. For production, this means on the one hand smaller quantities in production if production is not to be made to stock, and on the other hand more frequent retooling of the systems in order to be able to manufacture the different product variants. For the first time, three Kufstein-based companies - Freudenberg Sealing Technologies, Pirlo Metallverpackungen and STHIL Austria - are facing the same challenges and learning from each other in the process.
FAST RETOOLING TO INCREASE CUSTOMER SATISFACTION
The aim of the SMED methodology is to be able to switch machines from the manufacture of one product to that of another as quickly as possible. This is where the terminology single minute exchange of dies comes from. In order to achieve this, those set-up activities that can be carried out while a system is still in operation are identified. Tools are then used to speed up the remaining tasks. The set-up processes are filmed, broken down into their individual steps and improved using a simple four-step method: separating internal and external set-up processes, transferring internal to external set-up processes, optimising and standardising internal and external set-up processes and eliminating adjustment processes.
FROM HEAD TO HAND - IMMEDIATE IMPLEMENTATION OF WHAT HAS BEEN LEARNT
In small, cross-company groups, the participants practised immediately recognising and eliminating waste in a set-up process for a plastics printing system in the laboratory. Not only did they significantly improve the exercise process, they also reflected on the situations in their own companies and considered measures to reduce set-up times even further. With the knowledge they have acquired, they can now help to increase flexibility in production in order to fulfil changing customer requirements.